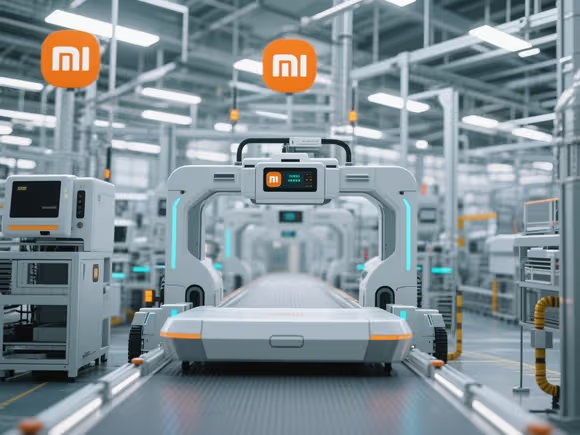
一、无人工厂的技术架构
1. 核心工艺的极致自动化
- 一体化压铸技术:工厂配备全球最大的 9100 吨压铸岛集群,可在 120 秒内完成后地板等大型部件的压铸,相比传统工艺减少 70% 的零部件数量和 30% 的生产工时。这一技术由小米自研,结合亚威股份等供应商的精密机床,实现了铝镁合金材料的超精密成型。
- 车身车间黑灯生产:400 余台协作机器人组成柔性生产线,通过视觉识别和力控技术完成钢铝混合车身的焊接、铆接和涂胶,综合自动化率达 91%。其中,269 台连接机器人实现车身骨架 100% 全自动组装,36 台机器人完成四门两盖的高精度装调,误差控制在 ±0.5 毫米以内。
- 涂装工艺的微米级控制:德国七轴喷涂机器人配合 AI 视觉系统,实现油漆液滴的微米级分散,漆面厚度误差小于 0.1 微米。车间内的 AMR 物流车自动运输零部件,减少人工干预带来的污染风险。
2. AI 驱动的质量闭环
- X-Eye 智能质检系统:对每个压铸部件进行 28 次 X 光扫描,通过深度学习算法检测内部缺陷,准确率达 99.9%,效率是传统人工检测的 20 倍。该系统已申请 23 项专利,覆盖压铸件、焊点、漆面等全维度检测。
- 激光雷达在线检测:在车身车间部署 400 多个高精度摄像头,结合激光雷达实时扫描车身轮廓,检测精度达 0.05 毫米,数据自动反馈至工艺系统进行参数修正。
- 整车级 AI 诊断:下线车辆通过 2.5 公里测试跑道时,车载智能系统自动完成动力、底盘、自动驾驶等 127 项功能测试,数据同步上传云端进行健康评估。
二、生产效率与成本优势
- 76 秒下线速度:通过工序并行优化和物流路径缩短,工厂实现每 76 秒生产一台整车,产能利用率达 92%,高于行业平均的 80%。这一效率在新能源汽车领域仅次于特斯拉上海工厂的 30 秒 / 辆,但在多车型混流生产方面更具灵活性。
- 人力成本压缩:工厂仅需 100 名技术人员负责设备维护和系统监控,相比传统工厂减少 80% 的人力需求。这些人员通过 AR 眼镜和数字孪生系统远程操控生产线,实现 “少人化” 管理。
- 绿色制造实践:车间顶部的光伏板每年发电 1640 万度,满足 20% 的生产用电需求;废水处理系统实现 99% 的重金属回收,固体废弃物综合利用率达 95%。
三、行业对标与技术突破
1. 与特斯拉的差异化竞争
- 工艺创新:小米的 9100 吨压铸机比特斯拉的 9000 吨设备吨位更大,可生产更复杂的车身结构件;而特斯拉的 4680 电池生产线自动化率更高,达到 95%。
- 智能化深度:小米将智能座舱和自动驾驶技术深度融入生产流程,例如在总装车间利用自研的澎湃 OS 系统进行整车功能调试,而特斯拉更多依赖第三方软件生态。
2. 供应链自主化突破
- 核心部件自制:工厂自建电池车间生产 CTB 电池,采用倒置电芯技术提升 48% 的碰撞安全性;电机车间实现 V8s 电机的 27200 转 / 分钟超高速运转,性能超越保时捷 Taycan。
- 设备国产化率:冲压线、压铸机等关键设备 70% 来自国产供应商,相比外资品牌 50% 的国产化率,显著降低了设备采购成本。
四、未来演进方向
- 二期工厂升级:2025 年投产的二期工厂将引入 5G+MEC 边缘计算系统,实现设备间的微秒级协同;同时部署数字孪生工厂,实时模拟生产过程,将换型调试时间从 8 小时缩短至 2 小时。
- 无人物流网络:规划中的 AGV 车队将连接仓储、生产和测试环节,利用北斗定位和视觉导航实现全流程无人运输,预计减少 30% 的物流人力。
- 碳足迹管理:计划 2026 年实现工厂运营碳中和,通过绿电采购、碳捕捉技术和供应链低碳改造,将单车碳排放强度降低至 15 吨 CO₂以下。
这座 “黑灯工厂” 的背后,是小米对智能制造的深度思考:通过技术创新重构生产要素,将汽车制造从劳动密集型转向知识密集型。正如奥地利外交官在参观后所言:“小米汽车工厂展示了中国智造的新高度,其自动化水平和创新速度令人震撼。” 这种模式不仅为小米汽车的品质和成本控制奠定基础,更可能成为全球汽车工业智能化转型的新范式。
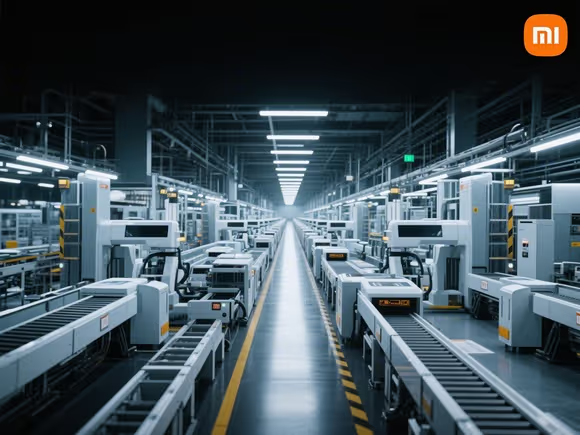