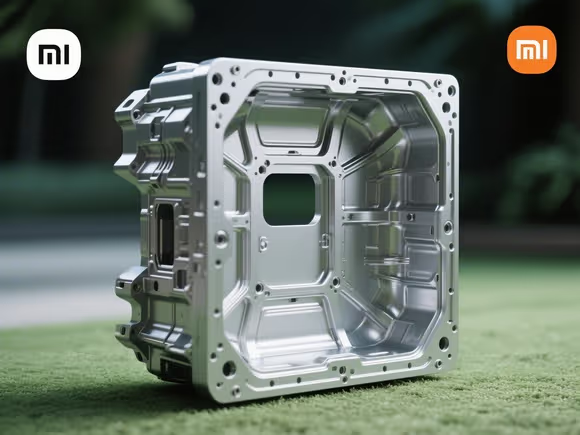
一、技术应用:从 SU7 到未来车型的全栈自研
- SU7 的突破性实践
小米 SU7 的后地板采用 9100 吨锁模力的压铸机集群,将 72 个零部件集成压铸为一体,焊点减少 840 个,减重 17%,生产工时缩短 45%。这一技术配合自研的 “小米泰坦合金”(一种含稀土、锆等元素的铝合金),使整车扭转刚度达到 51000N・m/deg,远超传统燃油车两倍。此外,三段式防撞设计在中低速碰撞时只需更换缓冲溃缩区,维修成本与传统工艺持平。
- 全产业链自研能力
小米不仅自研压铸机(与海天联合研发),还构建了覆盖材料、模具、工艺的全栈技术体系。例如,通过 AI 仿真系统从 1016 万种配方中筛选出泰坦合金,并自建压铸工厂实现 433 项工艺参数的闭环控制。这种 “设备 + 材料 + 工艺” 的垂直整合,使其成为国内唯一同时拥有量产自研压铸材料和设备的车企。
- 未来车型规划
2025 年推出的 SUV “昆仑” 将延续一体化压铸技术,进一步扩展应用范围。虽然具体参数未公开,但小米已在 SU7 基础上验证了大尺寸、长流程压铸的可行性,未来或向车身更多部位(如前舱、电池舱)延伸。
二、核心优势:效率、安全与成本的三重突破
- 生产效率跃升
小米压铸集群的单台设备每小时可生产 40 件压铸件,相比传统冲压焊接工艺效率提升 79 倍。配合视觉大模型检测系统,2 秒内完成微米级缺陷检测,良品率达到行业领先的 95%。
- 安全性与轻量化平衡
泰坦合金的抗拉强度达 350MPa,延伸率 12%,且可加入 30% 循环铝,实现碳减排 352.53kg / 件。一体化后地板通过 90km/h 后碰测试,为乘员舱提供更强防护。
- 成本控制能力
相比传统工艺,SU7 后地板生产减少 45% 工时,材料利用率提升至 90% 以上。虽然初期设备投资较高(9100 吨压铸机成本约 2 亿元),但规模化生产后可摊薄成本。西部证券测算,当产能达 10 万辆 / 年时,毛利率可达 25%-30%。
三、行业对比:吨位、材料与生态的竞争
- 与特斯拉的差异化路径
特斯拉虽率先应用一体化压铸(Model Y 后地板),但小米在材料和工艺上实现突破:泰坦合金无需热处理,而特斯拉需通过增加厚度补强;小米的三段式设计兼顾维修经济性,而特斯拉压铸件一旦损坏需整体更换。此外,小米 9100 吨压铸机吨位虽不及小鹏 12000 吨,但通过集群协同和材料优化实现性能超越。
- 国内新势力的技术博弈
小鹏 X9 采用 12000 吨压铸机集成 167 个零件,极氪 009 通过 7200 吨压铸机实现中段 “蜻蜓结构”,问界 M9 则以 9000 吨压铸机打造 “玄武车身”。小米的优势在于材料自研和全栈技术闭环,例如泰坦合金的轻量化和可回收性,以及压铸集群的参数精准控制。
- 传统车企的跟进与局限
大众、奥迪等传统车企虽布局一体化压铸,但受限于现有产线改造难度,更多用于局部结构件(如车门框架)。丰田则明确表示不采用特斯拉的 “千兆压铸” 方案,转向其他轻量化技术。
四、挑战与未来展望
- 技术瓶颈
超大吨位压铸机的模具寿命(通常约 10 万次)和良品率仍是难点。小米通过自研闭环温控系统(232 个回路精确控制)和模芯表面处理技术,将模具寿命提升至行业平均水平的 2 倍。
- 市场风险
一体化压铸的高固定成本要求车企具备规模效应。小米计划 2025 年实现 30 万辆交付目标,需确保产能爬坡顺利。此外,用户对维修成本的担忧仍需通过保险政策或模块化设计缓解。
- 技术演进方向
小米正探索 “整车一体化压铸”,目标将白车身零部件从 300 余个缩减至 5-6 个。同时,其研发的 16000 吨压铸机已进入测试阶段,未来或应用于更大尺寸车型。
总结
小米汽车的一体化压铸技术,是其 “软件定义硬件” 理念在制造端的延伸。通过材料、设备、工艺的全栈自研,小米不仅实现了生产效率和产品性能的跃升,更构建了差异化的技术壁垒。尽管面临模具成本、维修经济性等挑战,但其技术路径已得到行业认可(中国汽车工程学会认证为 “国际先进水平”)。随着产能释放和技术迭代,一体化压铸有望成为小米汽车的核心竞争力之一,推动其在新能源赛道的持续突破。
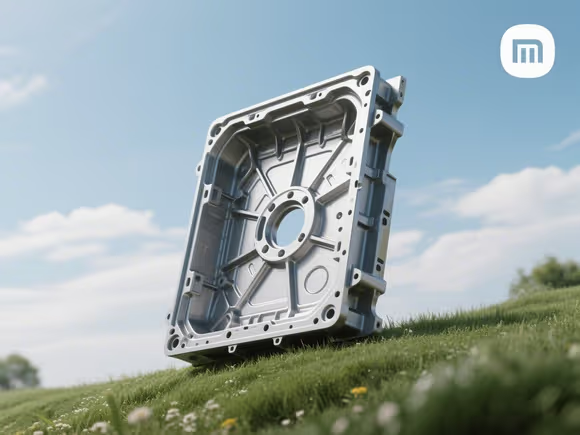