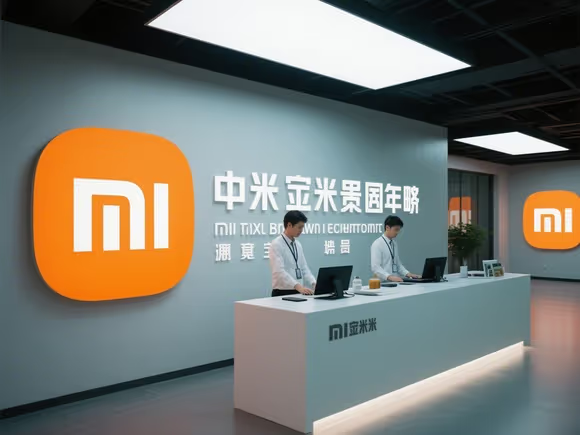
一、核心工厂:智能制造的标杆
- 北京昌平智能工厂
作为小米首个自有大规模工厂,昌平园区总建筑面积 8.1 万平方米,2024 年投产以来已实现年产 1000 万台高端旗舰手机的产能。工厂采用 “数据驱动 + 柔性敏捷” 的生产模式,96.8% 的组测包装备自研,软件 100% 自主开发,生产线上 90% 的工序由智能机器人完成,日均产量达 3 万台。例如,小米 14 系列的限量定制色 “海湾蓝” 和 “橄榄绿” 均在此生产,其工艺创新验证环节通过数字孪生技术实现参数智能调优,良率提升至 99.95%。
- 北京亦庄汽车工厂
小米汽车的核心制造基地,一期设计年产能 15 万辆,2024 年交付超 13 万辆,二期扩建至 105 公顷后总产能将达 30 万辆。工厂配备 9100 吨一体化压铸设备,每 120 秒生成一个压铸件,车身车间自动化率高达 91%,400 余台机器人实现 “黑灯生产”。环保方面,屋顶光伏电站年发电量 1640 万千瓦时,减少碳排放 9905 吨,相当于种植 54 万棵树。
- 武汉智能家电工厂
小米首个空调生产基地,2025 年 11 月投产后初期产能 300 万台 / 年,其中空调占比 50% 以上,配套 100 余间实验室实现 “研发 - 生产” 闭环。工厂采用 AI 质检技术,通过空气流动特征比对算法检测滤网脏堵,准确率提升至 99.8%,制冷剂不足检测效率提高 20 倍。
二、技术创新:重新定义制造范式
- 全流程数智化
昌平工厂部署自研工业数智平台,打通从订单到交付的全链路数据,实现生产排程、工艺管理、装备维护的自动化。例如,通过 AI 预测性维护算法,射频探针寿命预测误差率低于 5%,减少停机损失 10%。
- 绿色制造技术
汽车工厂采用废水循环系统,中水回用率 50%,电泳槽清洗水超滤回收减少 80% 新水用量;昌平工厂通过智能厂务系统优化能耗,空调系统能耗降低 18%。
- 柔性生产能力
昌平工厂的 “平台 + 模块” 产线设计,可在 2 小时内完成不同机型换线,混线生产效率比传统产线提升 40%。
三、全球化布局:贴近市场的生产网络
地区 | 工厂类型 | 核心产品 | 产能规模 |
---|---|---|---|
印度 | 智能手机 / 电视 | Redmi 系列、小米电视 | 7 座工厂,年产能超 3900 万台 |
越南 | 智能手机 | Redmi Note 系列 | 太原省工厂月产能 200 万台 |
印尼 | 智能手机 | POCO 系列 | 芝卡朗工厂年产能 100 万台 |
巴西 | 智能手机 / 电视 | 小米 12T、小米电视 | 圣保罗工厂年产能 50 万台 |
海外工厂采用 “本地化 + 区域辐射” 策略,例如印度工厂 95% 的员工为女性,越南工厂 70% 的零部件来自本地供应链,显著降低物流成本。
四、供应链管理:效率与韧性的平衡
- 代工厂协同
小米 74% 的手机依赖代工厂,主要合作伙伴包括富士康(组装)、龙旗(ODM 设计)、闻泰(中低端机型),通过 “动态评级 + 技术赋能” 模式确保品控。例如,空调代工由长虹、TCL、海信分工,长虹负责基础款,TCL 主攻中高端,形成互补。
- 垂直整合
自研澎湃芯片、CTB 电池等核心技术,武汉工厂实现空调压缩机自产,成本降低 15%。
- 风险防控
建立供应链自然灾害预警系统,整合气象数据预测台风、洪水等风险,2024 年成功规避印度工厂暴雨导致的停工风险。
五、可持续发展:从合规到引领
- 碳中和路径
承诺 2040 年实现自身运营碳中和,2030 年碳排放较基准年减少 30%。2023 年,昌平工厂光伏发电占比 30%,包装塑料使用量减少 60%。
- 绿色产品设计
小米 14 Pro 后盖采用生物基尼龙,碳足迹降低 20%;空调产品通过 AI 节能算法,能效较行业平均提升 36.9%。
- 供应链 ESG
要求供应商通过 RBA 认证,2024 年对 300 家供应商进行 ESG 审核,淘汰 12 家不符合标准的企业。
总结:制造能力的战略价值
小米工厂不仅是产品生产基地,更是技术验证与生态协同的平台。通过 “自研 + 代工” 双轮驱动、“全球布局 + 区域深耕” 的制造网络,以及 “效率优先 + 可持续发展” 的运营理念,小米正从互联网公司向智能制造巨头转型。未来,随着武汉家电工厂投产和汽车产能释放,小米将进一步巩固在 “人车家全生态” 领域的制造优势。
