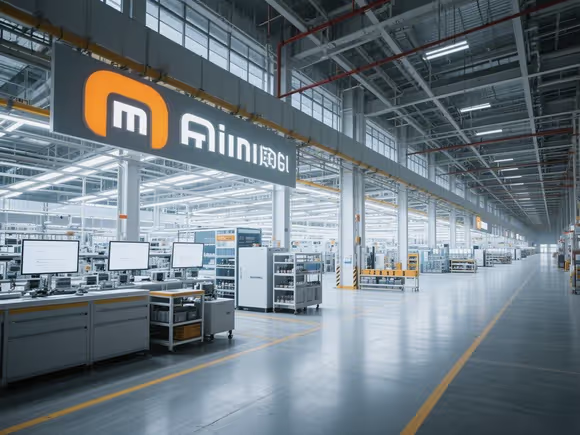
一、工厂概况:智能化与绿色化的标杆
- 地理位置与规模
工厂位于北京经济技术开发区(亦庄)马驹桥智能制造基地,总占地面积约 143 公顷(一期 72 万㎡,二期 53 万㎡,扩建后 105 万㎡)。这一选址依托亦庄成熟的汽车产业链生态,周边聚集了宁德时代、比亚迪等核心供应商,70% 的零部件可实现京津冀区域内供应。
- 生产工艺与自动化
工厂涵盖冲压、焊接、涂装、总装四大传统工艺,同时自建大压铸和电池车间,实现车身一体化压铸(最大零件尺寸 1.7 米)和电池 Pack 自主生产。全厂部署超 700 台工业机器人,关键工艺自动化率达 100%,车身焊接精度控制在 ±0.5 毫米,每 76 秒即可下线一台小米 SU7。
- 研发与测试设施
工厂内建有 29 个研发实验室,包括电池安全实验室、自动驾驶仿真实验室等,并配备 2.5 公里长的测试跑道,涵盖高速环道、湿滑路面、越野地形等 18 种测试场景,可满足车辆全生命周期验证需求。
二、产能规划:从 15 万到 35 万的跨越
- 一期工厂进展
一期于 2022 年 4 月开工,2023 年竣工,设计年产能 15 万辆。2024 年实际交付 13.68 万辆,产能利用率超 90%,单月交付峰值突破 2.9 万辆(2025 年 3 月)。
- 二期工厂升级
二期于 2024 年 7 月开工,2025 年 4 月完成规划验收,6 月竣工后将新增 15 万辆年产能,总产能提升至 30 万辆。扩建后工厂面积将达 105 公顷,预计 2026 年产能可进一步提升至 50 万辆,支撑小米冲击百万辆年销目标。
- 供应链保障
核心供应商包括宁德时代(三元锂电池)、比亚迪(磷酸铁锂电池)、联合电子(驱动电机)、德赛西威(智能座舱)等,同时通过投资瑞隆科技(电池回收)、云山动力(大圆柱电池)等企业布局产业链上下游。
三、技术创新:从硬件到软件的全栈自研
- 关键技术突破
- 大压铸工艺:采用自研免热处理合金材料,单次压铸成型后底板零件数量从 70 个减少至 1 个,生产效率提升 40%,车身重量降低 10%。
- 电池技术:与宁德时代合作开发 800V 高压平台,支持 15 分钟充电续航 400 公里,同时布局钠离子电池和固态电池技术。
- 自动驾驶:搭载 Orin-X 芯片和激光雷达,支持城市领航辅助驾驶(City NOA),2025 年将通过 OTA 升级至完全自动驾驶(L4)。
- 智能生态融合
工厂生产的小米 SU7 系列车型深度整合小米澎湃 OS 系统,支持手机与车机无缝互联、语音助手跨设备唤醒、智能家居远程控制等功能,构建 “人车家全生态”。
四、环保实践:绿色制造的示范样本
- 能源管理
屋顶铺设 16.2 兆瓦分布式光伏电站,年发电量 1640 万度,可满足工厂 10% 的用电需求,相当于减少 1.28 万吨 CO₂排放(约合 54 万棵树)。
- 三废处理
- 废水:采用 “预处理 + 混合污水处理 + 中水回用” 工艺,重金属零排放,循环用水比例达 50%,电泳槽清洗水回收率超 80%。
- 废气:涂装车间废气经 RTO 焚烧处理,VOCs 去除率超 99%,排放浓度仅为国标 1/5。
- 固废:废铝、废钢等金属 100% 回收,塑料件破碎后重新造粒,危险废物委托专业机构无害化处理。
- 绿色供应链
要求核心供应商 2025 年前实现 100% 可再生能源使用,并通过碳足迹管理系统追踪全价值链碳排放,目标 2040 年达成自身运营碳中和。
五、未来布局:从单一工厂到产业集群
- 新车型规划
2025 年 6-7 月将推出中大型 SUV 小米 YU7,搭载单电机(235kW)和双电机(508kW)版本,续航超 700 公里;同时计划量产 SU7 Ultra 赛道版,搭载三电机四驱系统,零百加速 1.9 秒,挑战纽北最速量产车纪录。
- 全球产能扩张
武汉工厂已启动建设,规划年产能 30 万辆,主要生产经济型车型;欧洲工厂选址进入最后阶段,预计 2026 年投产,辐射欧盟市场。
- 产业协同效应
工厂周边规划建设新能源汽车零部件产业园,吸引电控系统、智能网联设备等企业入驻,形成 “研发 - 生产 - 物流” 一体化生态,预计 2025 年配套产能达 37 万辆。
总结
小米汽车北京超级工厂不仅是一座高效智能的制造基地,更是小米集团践行 “铁人三项” 战略(硬件 + 新零售 + 互联网)的重要支点。其 76 秒下线一台车的生产效率、100% 自动化率、光伏覆盖的绿色工厂设计,以及自研大压铸、800V 高压平台等技术突破,均展现出小米在汽车领域的野心与实力。随着二期工厂投产和新车型上市,这座 “超级工厂” 将成为中国智能电动汽车产业的新标杆,推动小米从手机厂商向全球科技巨头的转型。
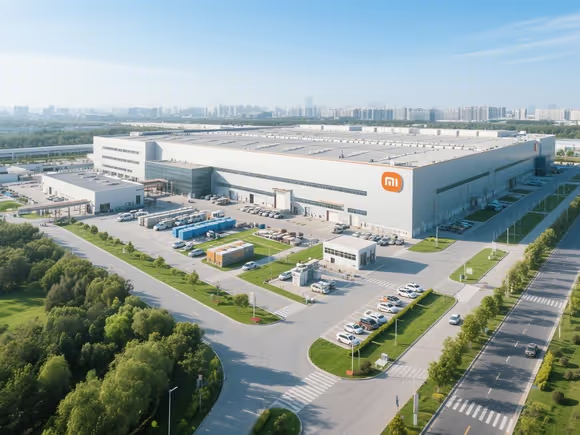