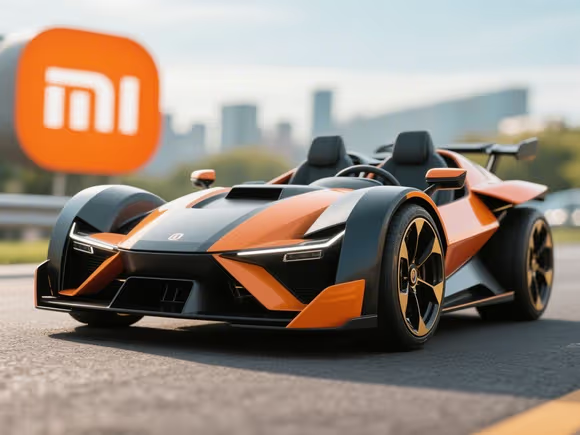
一、工厂布局:智能化与产能扩张并进
- 北京亦庄超级工厂
小米汽车一期工厂于 2024 年 3 月正式投产,是中国品牌唯一集研发、制造、交付和体验为一体的综合汽车科技产业园区,占地面积 72 万平方米,年产能规划 30 万辆。工厂采用摩德纳平台架构,聚焦低趴车型研发,实现人 - 车 - 家生态联动。
- 生产效率:焊装自动化率 100%,总装车间每 76 秒可完成一辆 SU7 的组装,车间内物流机器人自动运输零件,整车下线后需通过 16 种路况测试。
- 绿色制造:工厂配备光伏发电系统,符合 “智能绿色工厂” 定位。
- 产能扩张计划
- 二期工厂:位于北京亦庄,与一期工厂相邻,2024 年 7 月拿地,预计 2025 年年中竣工,投产后年产能将提升至 50 万辆。
- 三期规划:二期工厂旁 52 公顷地块已公示为工业用地,未来可能成为三期工厂选址,助力 2026 年实现年产销 100 万辆目标。
- 武汉工厂:2025 年 4 月确认落户武汉经开区,占地 2000 亩,与小鹏、路特斯为邻,预计 2026 年投产。
二、生产工艺:自动化与柔性化结合
- 核心工艺
- 一体化压铸:采用自研 “泰坦合金” 和免热处理材料,通过 232 个回路的闭环温控系统,实现车身大件自动化装配精度 ±0.5 毫米,超越豪华品牌标准。
- 电池组装:与宁德时代合作开发 CTB 一体化电池技术,电池包与车身结构融合,体积利用率达 77.8%,支持 800V 高压平台,充电 15 分钟续航增加 500km。
- 电子域控制器:思灵机器人提供柔性组装线,10 台机器人完成物料抓取、插连接器、理线束等工序,单位小时产量(UPH)高于行业平均水平 30%。
- 内饰与总装
- 自动化:车身车间综合自动化率 91%,400 多台机器人配合 400 多个摄像头实现 “黑灯生产”。
- 人工参与:内饰组立(如座椅、中控台安装)仍需人工操作,但通过标准化流程确保装配一致性。
三、供应链管理:双供应商体系与生态协同
- 核心零部件供应商
- 电池:SU7 标准版采用比亚迪(弗迪电池)与宁德时代双供应商体系,随机混装;Pro 版和 Max 版搭载宁德时代三元锂电池,支持电芯倒置技术提升安全性。
- 电机:苏州汇川联合动力提供碳化硅电机,最高转速 21000rpm,功率密度 6.78kW/kg。
- 智能系统:英伟达 Orin 芯片支持 Xiaomi Pilot 智驾系统,SA8295P 座舱芯片实现 56 英寸 HUD 与小米澎湃 OS 深度互联。
- 生态链赋能
- 供应链整合:小米将消费电子供应链经验移植到汽车领域,与宁德时代、汇川技术等建立长期合作,同时通过投资补齐半导体、激光雷达等产业链环节。
- 成本控制:自研 CTB 电池技术降低成本 15%,规模化生产目标将单车毛利率从 18.5% 提升至 25%。
四、质量控制:全流程检测与用户反馈闭环
- 生产端
- 零部件检验:入厂零部件需通过 1050 项安全测试,电池包在 55℃高温下无明火、无热蔓延。
- 整车测试:下线车辆需经过 16 种路况测试,包括高速、越野、极端天气等,确保性能稳定性。
- 用户端
- 售后网络:截至 2025 年 3 月,全国建成 235 家门店、127 家服务网点,4 月计划新增 33 家门店。
- 用户反馈:尽管存在智能驾驶故障、车机系统卡顿等投诉,但部分用户对 SU7 的安全性表示认可,如坠崖事故后车主复购同款车型。
五、市场表现:销量冲刺与产能挑战
- 交付数据
- 2025 年 3 月交付量 2.9 万台,累计交付超 21.6 万台,订单积压约 21 万台,交付周期最长达 48 周。
- 2025 年目标 35 万辆,需每周交付约 6900 台,产能爬坡压力显著。
- 竞争格局
- 产品定位:SU7 标准版 21.59 万元起,主打 “豪华体验大众化”,对标特斯拉 Model 3;SU7 Ultra 定价 39.99 万元,配置逼近保时捷 Taycan。
- 市场排名:2025 年第 15 周交付 6280 辆,位列新势力第五,落后于小鹏、理想、问界、零跑。
总结:小米造车的 “互联网思维” 实践
小米汽车的组装生产体系体现了 **“技术自研 + 生态整合 + 快速迭代”** 的互联网逻辑:
- 优势:全流程自动化提升效率,供应链深度协同降低成本,智能化生态增强用户粘性。
- 挑战:产能瓶颈制约交付速度,质量稳定性与售后服务网络待优化,品牌溢价能力仍需验证。
未来,随着二期工厂投产和三期规划落地,小米汽车的产能与市场份额有望进一步提升,但能否在 “红海” 竞争中持续突围,仍取决于技术迭代速度与用户口碑积累。
