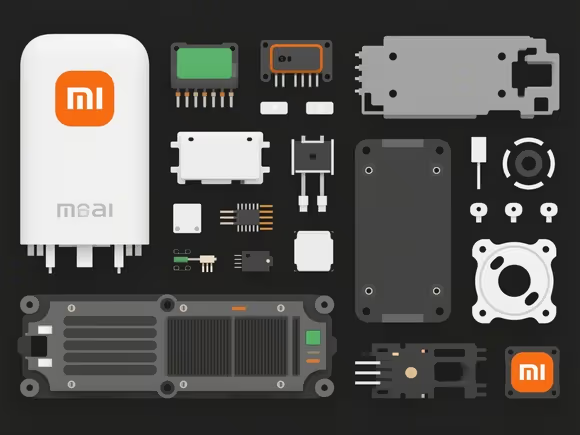
一、工厂布局:双基地协同,产能快速扩张
- 北京亦庄超级工厂
- 规模与产能:总投资 630 亿元,分两期建设。一期工厂 2023 年竣工,年产能 15 万辆;二期工厂 2025 年年中投产,新增产能 15 万辆,合计年产能 30 万辆。工厂采用 “黑灯生产” 模式,自动化率达 91%,每 76 秒可组装一辆 SU7。
- 技术亮点:
- 大压铸技术:配备 9100 吨压铸机,实现后地板一体化成型,焊点减少 70%,生产效率提升 30%。
- 智能检测:激光雷达检测车身精度达 0.05mm,X 光 AI 检测压铸件内部缺陷,准确率 99.9%。
- 电池组装:自研 CTB 电池技术,电池与车身一体化设计,体积效率提升 15%,续航增加 10%。
- 武汉工厂
- 规划与定位:总占地 2000 亩,毗邻小鹏、路特斯工厂,预计 2026 年投产,目标年产能 50 万辆,助力小米冲击百万销量目标。工厂将引入柔性生产线,兼容多车型生产。
二、生产流程:高度自动化与模块化
- 核心车间技术
- 冲压车间:6900 吨冲压线,精度达 0.1mm,每小时生产 600 个车身部件。
- 车身车间:400 台机器人协同作业,实现钢铝混合车身全自动焊接,焊点合格率 99.98%。
- 涂装车间:德国七轴喷涂机器人,漆面厚度误差 ±1μm,支持 12 种颜色快速切换。
- 总装车间:AGV 小车自动运输零部件,电池与车身合装精度 ±0.5mm,下线检测线模拟极端工况测试。
- 柔性化生产
- 电子域控制器组装线:思灵机器人打造,10 台机器人完成物料抓取、插连接器、理线束等工序,单位小时产量(UPH)提升 30%,换型时间仅 15 分钟。
- 模块化设计:电池、电机等核心部件采用标准化接口,支持不同车型快速切换,生产效率提升 20%。
三、供应链管理:全球化与垂直整合
- 核心供应商
- 电池:宁德时代提供三元锂电池(SU7 Max/Pro),比亚迪弗迪电池供应磷酸铁锂电池(标准版),小米自研电池 PACK 技术。
- 电机:联合汽车电子(后驱版)、苏州汇川(四驱版),自研电机效率达 97.5%。
- 智能化部件:华为提供自动驾驶芯片,蓝思科技供应中控屏,拓普集团提供空气悬架。
- 供应链策略
- JIT 模式:零部件库存周转天数压缩至 7 天,较行业平均水平减少 50%。
- 供应链金融:为中小供应商提供应收账款融资,缩短账期至 30 天,保障产能稳定。
- 自研关键技术:泰坦合金、800V 高压平台、碳化硅电驱等核心技术自主研发,降低对外依赖。
四、质量控制:全流程严苛标准
- 研发阶段
- 仿真测试:1000 万次虚拟碰撞测试,电池热失控模拟超 2000 小时,确保安全性。
- 样车验证:500 辆测试车累计路试超 1000 万公里,覆盖 - 40℃至 60℃极端环境。
- 生产阶段
- 工艺监控:每台设备配备传感器,实时采集温度、压力等数据,异常自动停机。
- AI 质检:100% 外观紫外光检测,0.05mm 精度识别划痕;X 光 AI 检测压铸件内部缺陷,效率提升 20 倍。
- 用户反馈
- OTA 升级:每周迭代软件,累计发布 12 次大版本更新,修复充电兼容性等问题。
- 售后网络:全国 28 城交付中心,48 小时故障响应,电池终身质保。
五、产能挑战与未来规划
- 当前瓶颈
- 订单积压:2025 年 4 月存量订单超 15 万辆,SU7 标准版交付周期达 37-40 周。
- 供应链压力:宁德时代、博世等供应商产能紧张,部分零部件交付延迟。
- 应对措施
- 扩产计划:北京二期工厂 2025 年年中投产,武汉工厂 2026 年建成,总产能将达 80 万辆。
- 技术升级:自研 4695 大圆柱电池,能量密度提升 20%,2025 年量产。
- 全球化布局:印度、东南亚工厂筹备中,目标 2026 年海外销量占比 30%。
总结
小米汽车的组装体系以 “智能制造 + 生态协同” 为核心,通过高度自动化工厂、垂直整合供应链和严苛质量控制,实现了从 “造车新势力” 到 “量产实力派” 的跨越。未来,随着武汉工厂投产和技术迭代,小米有望在 2026 年冲击百万销量,成为全球新能源汽车市场的重要参与者。
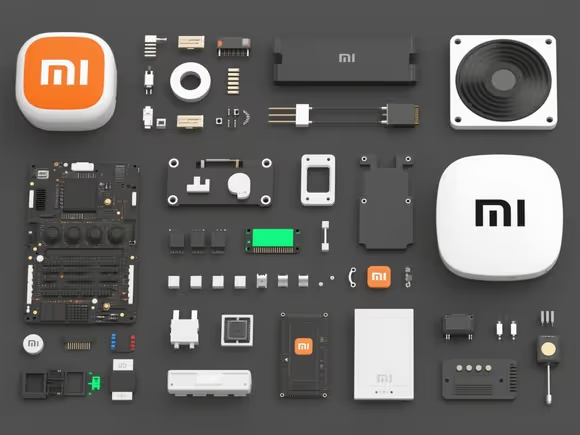